The In-House Difference
From piping design to fabrication, transportation, installation, and start-up and maintenance, JDP Mechanical completes all phases of the production process in-house. This gives us complete control over the quality and schedule of our system installations.
Our experienced Project Management team works closely with our clients to ensure on-time and on-budget delivery.
From drafting and design, to fabrication and transportation, to phased installation of rough-in work equipment, to the final location of electric fixtures, project managers coordinate all aspects of an engagement.
They schedule weekly meetings with all relevant stakeholders, as well as ensure that all project documents (equipment logs, shop drawings and progress schedules) are constantly updated.
Our in-house Design and Drafting department works with clients, architects, and construction managers to develop custom solutions to meet complex architectural requirements. Whether it's custom piping configurations for a tapered building like Via-57 or huge ice-chillers for a LEED platinum building like One Bryant Park, our engineers are up for the challenge.
JDP Mechanical's BIM Drafting Department takes piping design from contract drawings to intra-trade coordination all the way to shop drawings.
Our BIM Drafting allows for economical coordination, which assures space allocation for all trades and avoids costly field conflicts during installation.
Our drafting personnel have decades of experience and keep abreast of the latest improvements in drafting technology. Through continuing education, our engineers stay at the forefront of the rapidly changing landscape of energy-efficiency design.
JDP Mechanical is excited to announce we have expanded to an additional location in Ronkonkoma, New York. This new 18,000 Sq. Ft. facility includes modernized equipment and tools, ample storage space, and multiple offices for management and team building. Our piping specialists now operate using the latest products to assist in constructing our projects from inception.
This new space allows JDP to streamline our drafting, fabricating, and installation procedure with ease. We are looking forward to utilizing this location to enhance our ability to support New York City’s unwavering potential.
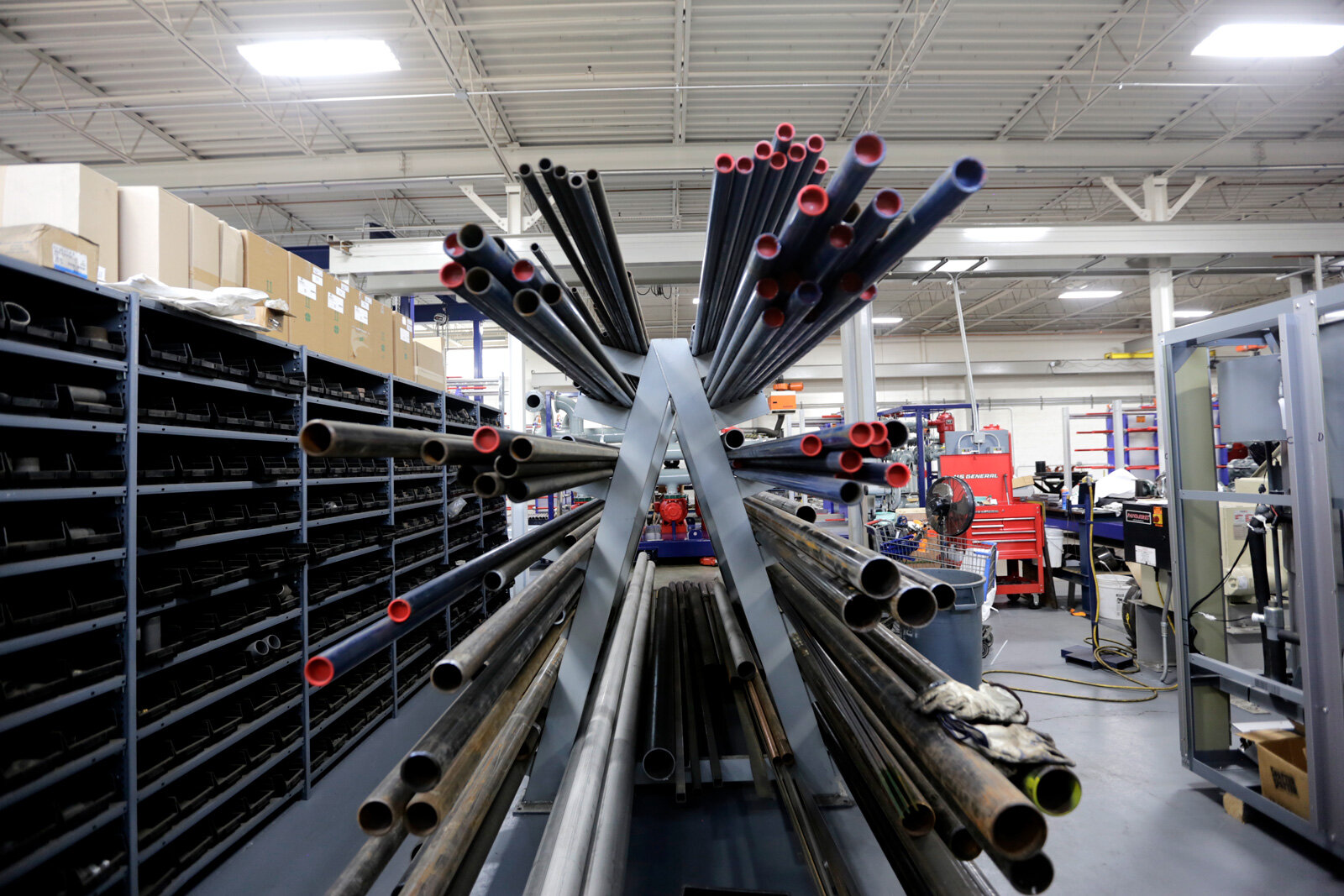
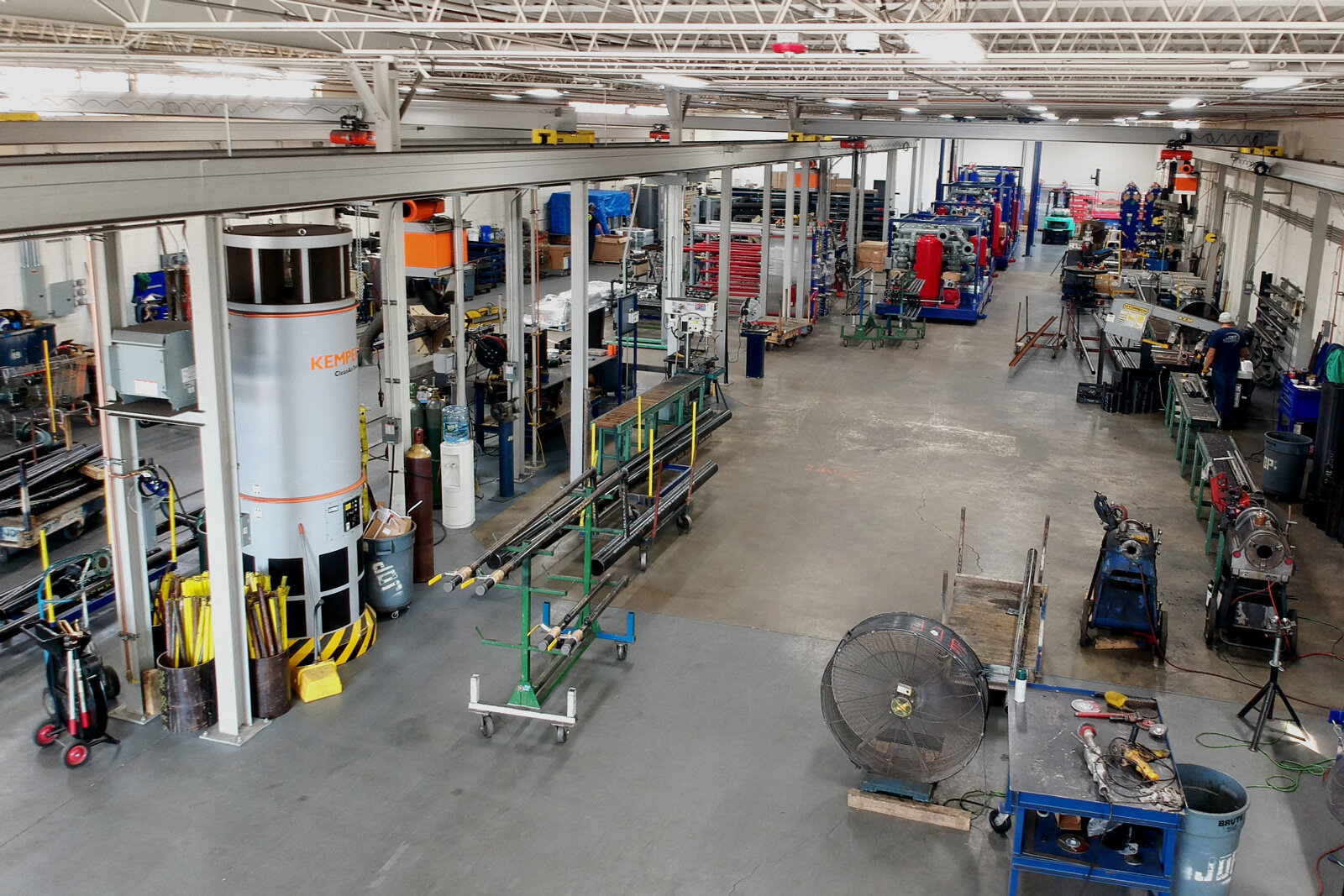

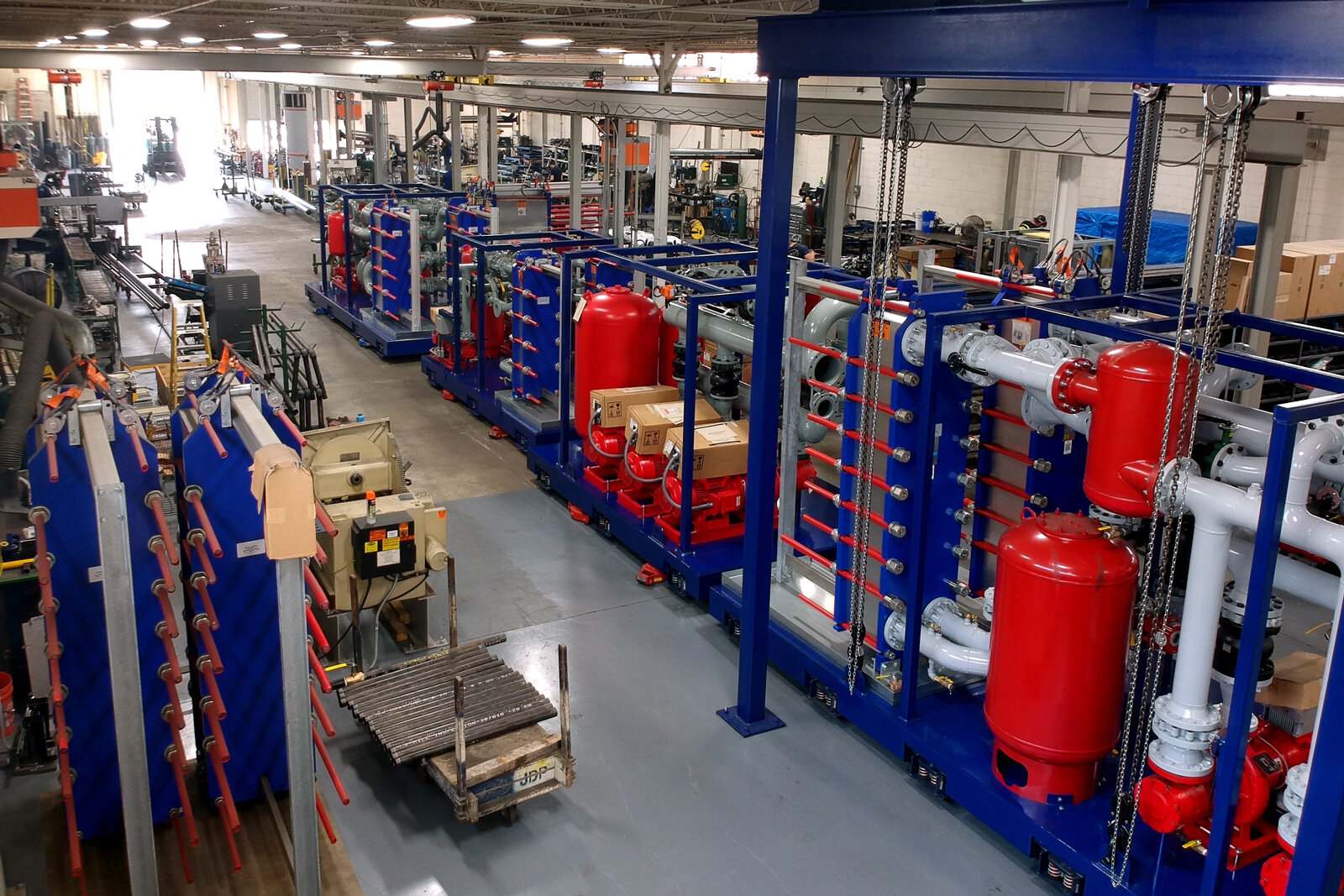
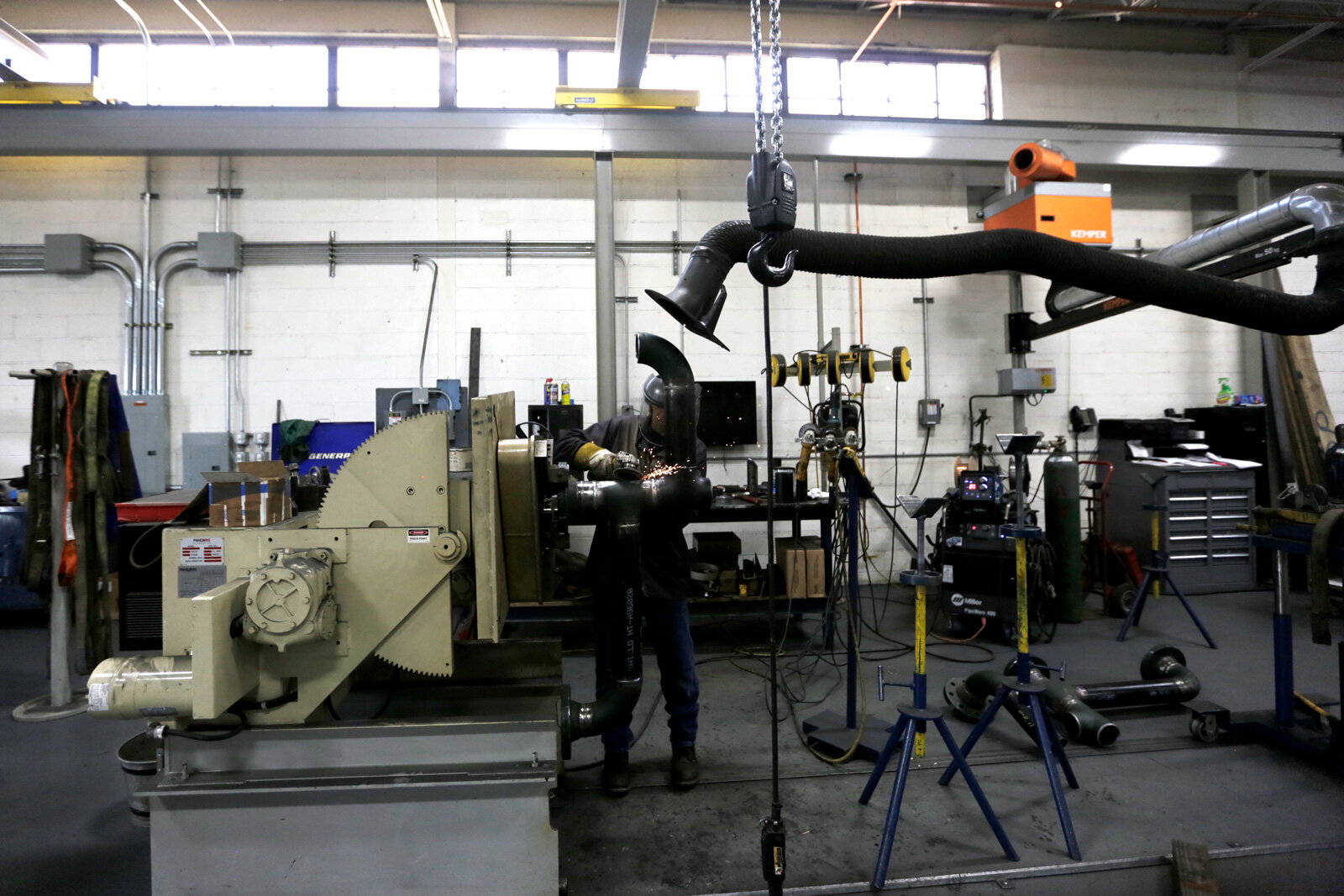
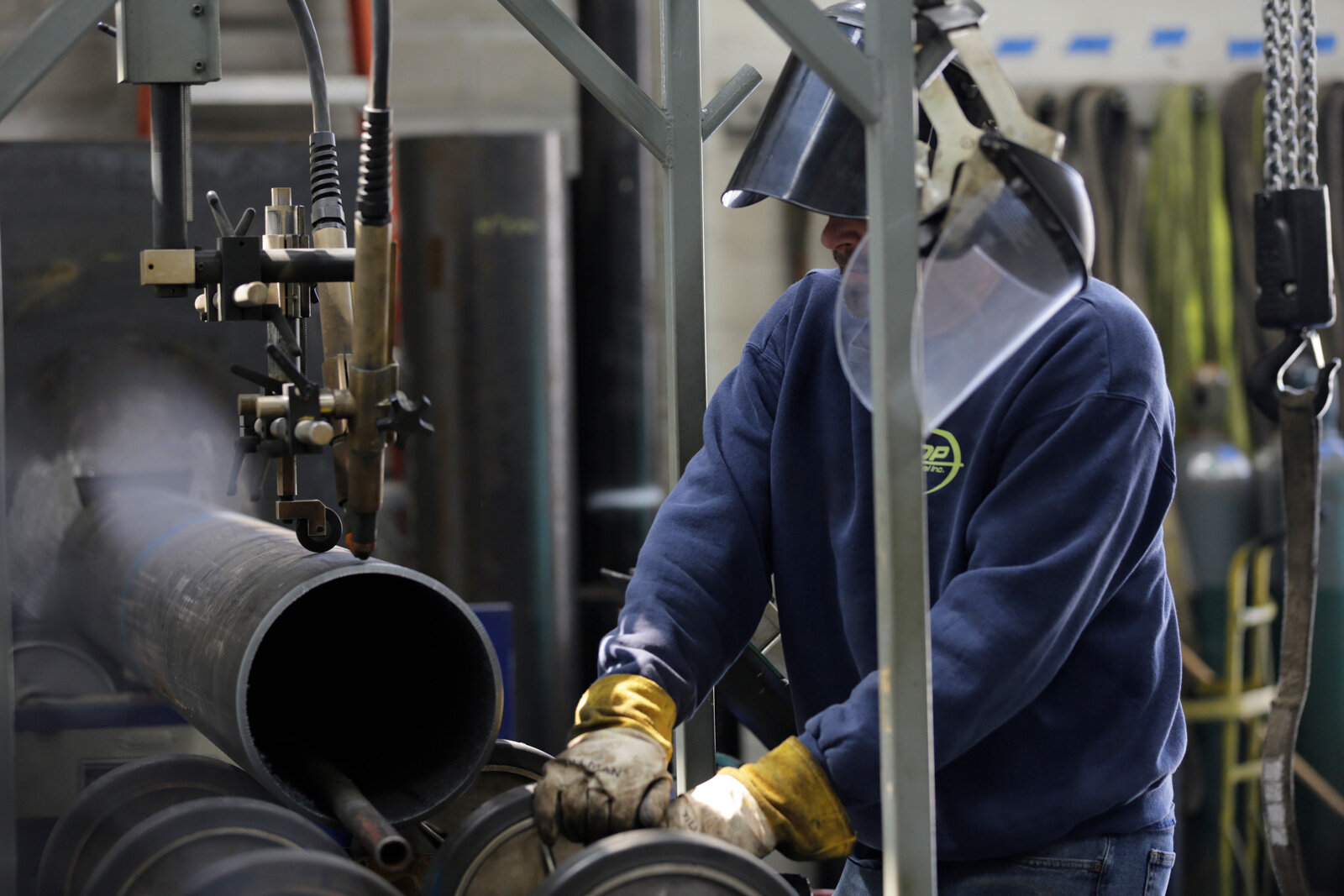
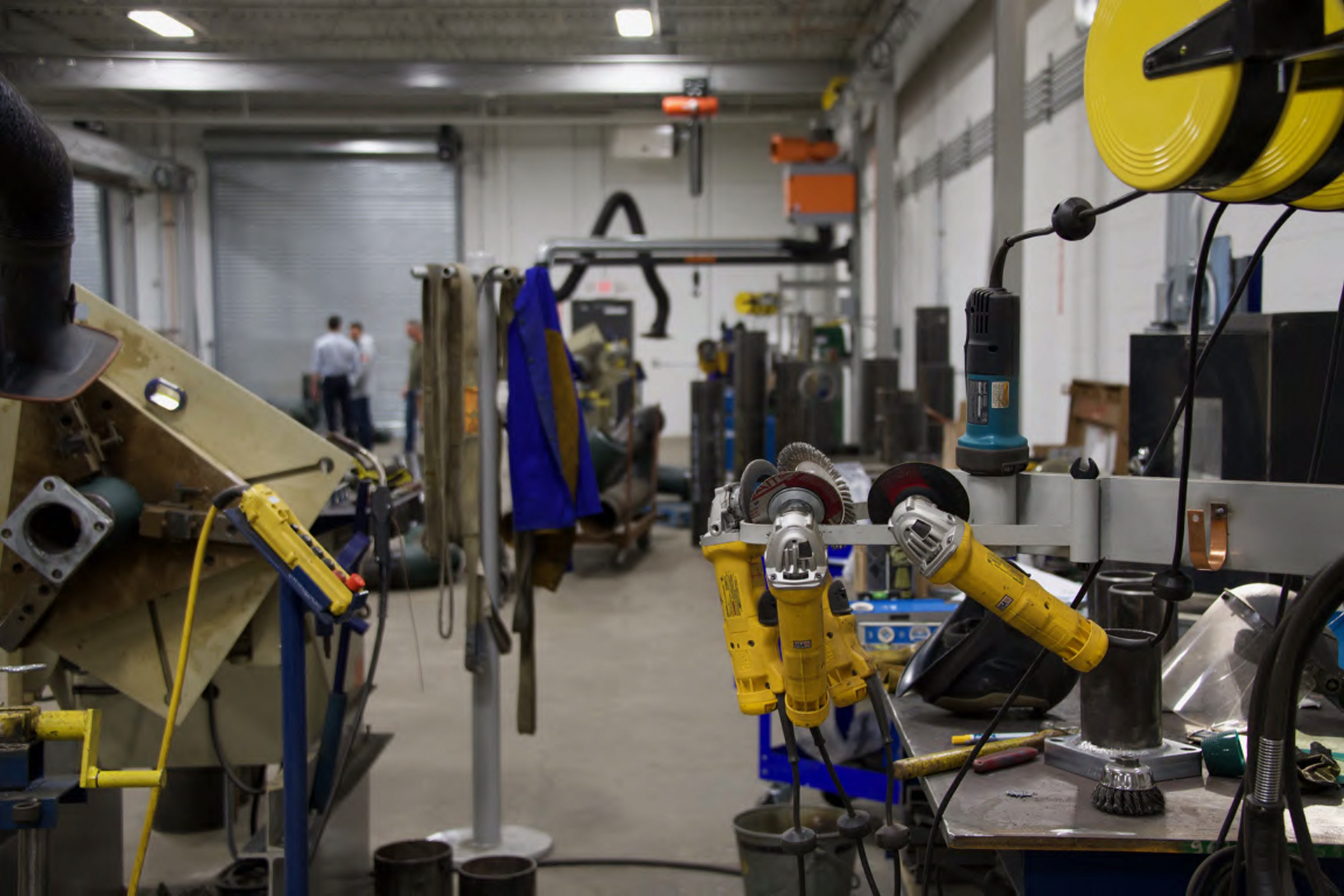

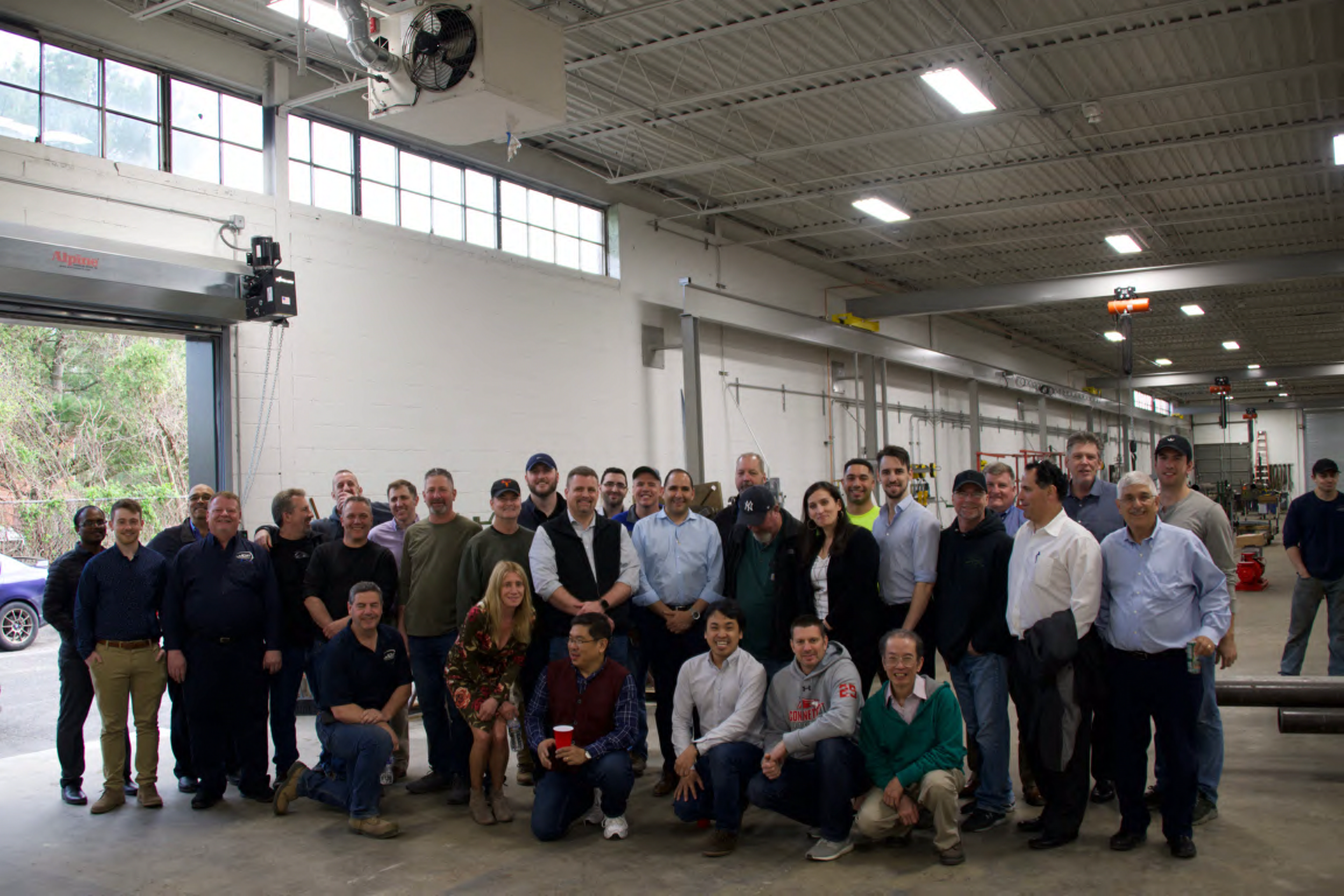
All prefabricated pipe is made in our shop and delivered by our trucks. Since we don't rely on external contractors, we have tight control over our production timelines.
Whether it's custom joints or specialized pipe configurations, our fabrication facility is set up for quick turn around.
Located in Astoria, NY, our close proximity to our job sites ensures that we can deliver solutions quickly.
Whether it's threading pipe through existing tunnels across the FDR, shipping custom ice-chillers via Metro North rail lines or leveraging multi-tier cranes for rooftop installations, we coordinate how best to transport and install our HVAC systems.
Our project team coordinates all rigging plans.
Handling of equipment and routing within the building is carefully planned long before the equipment arrives.
We also take a hands-on approach to system commissioning.
After installation is complete, JDP works closely with our clients during system commissioning. Our separate service department, with trained technicians, will be onsite to work through the typical start up problems.
Our maintenance staff is factory trained and equipment certified for most major manufacturers. We provide service and repairs on all equipment including Mitsubishi, Daikin, York, Trane, Carrier, Stultz, Liebert, Johnson Controls, Controls Systems, ABM, and more.
Building Maintenance
We specialize in the high-rise vertical market and provide services to both existing and new construction buildings.
Preventive Maintenance Contract Agreements are available, and all service customers receive priority service response times as defined within our maintenance agreements
Emergency Maintenance
Our certified and trained operations specialists are available 24/7/365 to address any issues that might come up.
All after-hours calls are received and routed through our dedicated answering service system.
JDP’s Safety Program includes a written safety manual, weekly meetings, and site-specific safety plans developed as necessary to address certain tasks (lock out, confined space, fall protections plans, and crane lifts.)
Our Safety policy was developed in accordance with Federal, State, and Local regulations, with particular emphasis on OSHA and EPA requirements that apply to our operations.
Employees at every level execute the company’s policy of maintaining a safe and healthy work environment.